MAS 2018 / 19

Nik Eftekhar, Rahul Girish, and Jonas van den Bulcke, photo credit: James Horkulak
rapid clay formations is a four-week design and build assignment investigating a novel fabrication process for malleable materials. Starting with the Remote Material Deposition installation in 2014, the Chair of Architecture and Digital Fabrication has investigated the idea of robotically positioning material in space from a distance and thereby creating differentiated architectural aggregations that are a direct expression of a dynamic and adaptive fabrication process. Continuing this concept, more recent projects developed within the MAS programme shifted the focus to the study of robotic fabrication processes for malleable materials, where the precise control of forces and positions applied to the material to design and build highly differentiated structures.
rapid clay formations invites the students to participate in a collaborative research where different groups investigate different aspects and potentials of the fabrication process. The setup consists of a small-scale six-axis robotic arm manipulating an end-effector that allows to prepare projectiles of different sizes, position them, and press them into their respective shapes by linear pneumatic actuation. Through iterations of empiric testing, design simulation, and physical prototyping different typologies of the technique were explored. Topics included the differentiation of force applied to the projectiles leading to different bonding behavior and thickness of the structure, the differentiation of projectile sizes (diameter and height) and their respective interlocking behavior, the discretisation of surfaces into single- and multi-layer high-resolution aggregations, and the possibility for different projectile topologies such as for example a torus shaped projectile. Besides showing the design potential of the different approaches, the goal was to increase the interlocking behavior of the projectiles that leads to better structural performance, to improve the robustness and speed of the fabrication process and to develop methods to relate the physical outcome to the computational design and simulation framework.

Nicolas Feihl, Sofia Michopoulou, and Keerthana Udaykumar, photo credit: James Horkulak

Nicolas Feihl, Sofia Michopoulou, and Keerthana Udaykumar, photo credit: James Horkulak

Noor Khader, Aya Shaker, and Yoana Taseva, photo credit: James Horkulak
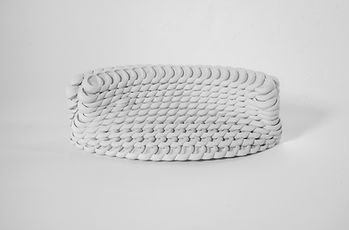
Noor Khader, Aya Shaker, and Yoana Taseva, photo credit: James Horkulak

Yuta Akizuki, Antonio Barney, and Chaoyu Du, photo credit: James Horkulak

Yuta Akizuki, Antonio Barney, and Chaoyu Du, photo credit: James Horkulak

Yuta Akizuki, Antonio Barney, and Chaoyu Du, photo credit: James Horkulak

Ying Shiuan Chen, Eleni Skevaki, and Wenqian Yang, photo credit: James Horkulak

Ying Shiuan Chen, Eleni Skevaki, and Wenqian Yang, photo credit: James Horkulak

Nik Eftekhar, Rahul Girish, and Jonas van den Bulcke, photo credit: James Horkulak

Ying Shiuan Chen, Eleni Skevaki, and Wenqian Yang, photo credit: James Horkulak

Nik Eftekhar, Rahul Girish, and Jonas van den Bulcke, photo credit: James Horkulak

Nik Eftekhar, Rahul Girish, and Jonas van den Bulcke, photo credit: James Horkulak
